Crystal oscillators, the heart of precise timing in electronics, undergo a meticulous manufacturing process. This journey begins with selecting and cutting high-purity quartz crystals, followed by shaping and polishing to achieve the desired resonant frequency.
Subsequent steps involve electrode deposition, packaging, and rigorous testing to ensure stability and accuracy. Understanding this complex process illuminates the precision embedded within these vital components, crucial for everything from smartphones to industrial systems.
What Are Crystal Oscillators
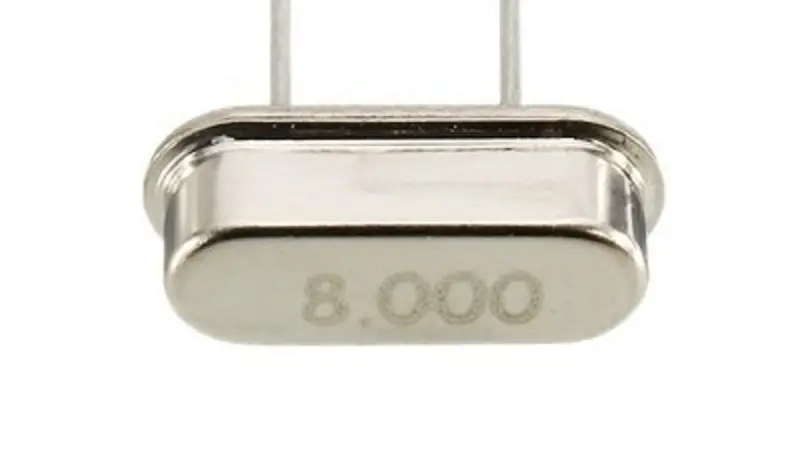
Crystal oscillators are electronic circuits that produce a precise and stable frequency signal by utilizing the piezoelectric effect of a quartz crystal. When voltage is applied to the crystal, it vibrates at its natural resonant frequency, which is determined by its physical dimensions and cut. This vibration, in turn, generates an electrical signal that can be used as a timing reference.
Essentially, the crystal acts as a highly selective resonator, ensuring that the oscillator maintains a consistent frequency output. The surrounding electronic circuitry amplifies and sustains these vibrations, creating a reliable clock signal. Crystal oscillators are fundamental components in a wide range of electronic devices, providing the timing accuracy needed for everything from microprocessors and communication systems to consumer electronics and industrial equipment.
Crystal Oscillator Manufacturing Process

Crystal oscillator manufacturing is a meticulous process, transforming raw quartz into precise frequency sources. It begins with careful crystal cutting, followed by electrode application and precise assembly. Rigorous testing and environmental sealing ensure reliability. Each stage contributes to the oscillator’s accuracy and stability, essential for modern electronics.
Step 1. Cutting
The initial stage involves precisely cutting raw quartz crystal into thin wafers of specific dimensions. This process demands extreme accuracy, as the crystal’s resonant frequency is directly tied to its physical dimensions. Specialized diamond saws, often wire saws or inner diameter saws, are employed to minimize material waste and ensure clean cuts. Critical parameters like thickness, angle, and surface finish are meticulously controlled to achieve the desired frequency characteristics. The crystallographic orientation of the cut is also vital, as it determines the temperature coefficient of the oscillator.
Achieving the precise dimensions of the crystal blank is challenging due to the inherent hardness and brittleness of quartz. The cutting process is often carried out in a controlled environment to prevent contamination and minimize thermal stress. The resulting wafers are then subjected to a series of cleaning and lapping processes to achieve the required surface finish and remove any surface imperfections. These imperfections, if left unchecked, could affect the crystal’s performance and long-term stability.
The selection of the crystal cut (AT-cut, BT-cut, etc.) determines the temperature stability of the oscillator. Each cut exhibits unique frequency-temperature characteristics, influencing the oscillator’s suitability for specific applications. The cutting process is therefore a critical step that lays the foundation for the oscillator’s overall performance. The precision of the cutting ensures the subsequent steps build upon a solid base, preventing cumulative errors that would compromise the final product.
Step 2. Silver Plating
Following the cutting and cleaning, the quartz crystal wafers undergo a silver plating process. This involves depositing a thin layer of silver onto the two major surfaces of the crystal. The silver electrodes serve as electrical contacts, enabling the crystal to oscillate when subjected to an electric field. The plating process must be carefully controlled to ensure uniform thickness and adhesion of the silver layer. Variations in plating thickness can affect the crystal’s resonant frequency and quality factor (Q-factor).
Several techniques can be used for silver plating, including vacuum deposition, sputtering, and electroless plating. The choice of technique depends on the desired plating thickness, uniformity, and adhesion. Post-plating treatments, such as annealing, may be performed to improve the adhesion and electrical conductivity of the silver layer. The silver plating process is a critical step in establishing the electrical characteristics of the crystal oscillator.
The quality of the silver plating directly impacts the crystal’s performance and reliability. A poorly plated crystal may exhibit high resistance, poor frequency stability, or even premature failure. The plating process is typically carried out in a cleanroom environment to minimize contamination and ensure the integrity of the silver layer. Monitoring the thickness and uniformity of the plating is essential to maintain consistent performance across all crystal oscillators.
Step 3. Dispensing
Dispensing involves the application of conductive epoxy or other adhesive materials to secure the crystal blank within its package. This crucial step ensures the crystal is mechanically stable and electrically connected to the package terminals. The dispensing process must be precise and controlled to prevent excess adhesive from interfering with the crystal’s oscillation or causing electrical shorts. Automated dispensing systems are often used to achieve consistent and accurate application of the adhesive.
The type of adhesive used and the dispensing pattern are carefully selected based on the crystal’s size, package type, and operating frequency. The adhesive must provide strong bonding strength, good electrical conductivity, and long-term stability. The dispensing process is often performed in a controlled environment to minimize contamination and ensure consistent adhesive properties.
The mechanical stability of the crystal is paramount for reliable operation. The dispensing process must ensure the crystal is securely fixed within the package, preventing movement or vibration that could affect its frequency stability. The dispensing pattern is designed to minimize stress on the crystal and ensure uniform adhesion. The precision of the dispensing process is a key factor in achieving high-quality and reliable crystal oscillators.
Step 4. Testing
Testing is an integral part of the crystal oscillator manufacturing process, ensuring each unit meets the required specifications. The initial testing phase involves measuring the crystal’s resonant frequency, resistance, and quality factor (Q-factor). These parameters are critical for determining the crystal’s performance and suitability for specific applications. Automated test equipment is used to perform these measurements quickly and accurately.
Subsequent testing phases may include temperature testing, shock testing, and vibration testing to evaluate the crystal’s performance under various environmental conditions. These tests are designed to simulate real-world operating conditions and ensure the crystal’s reliability and durability. The testing process is typically carried out in a controlled environment to ensure accurate and repeatable results.
The data collected during testing is used to identify any defects or deviations from the specifications. Crystals that fail to meet the required standards are rejected or reworked. The testing process is a crucial step in ensuring the quality and reliability of the final product. The rigorous testing regimen provides confidence in the oscillator’s ability to perform consistently in demanding applications.
Step 5. Seal Welding
Seal welding is the process of hermetically sealing the crystal oscillator package. This step is essential to protect the crystal from environmental factors such as moisture, dust, and contaminants, which can affect its performance and longevity. The sealing process involves welding a metal lid or cap onto the package base, creating an airtight enclosure. Laser welding, resistance welding, and seam welding are common techniques used for seal welding.
The seal welding process must be carefully controlled to ensure a strong and reliable seal without damaging the crystal. The welding parameters, such as power, time, and pressure, are optimized to achieve a consistent seal quality. The integrity of the seal is critical for maintaining the crystal’s performance over its lifetime.
A hermetic seal is vital for maintaining the internal environment of the crystal oscillator. It prevents moisture and contaminants from entering the package, which could lead to corrosion, frequency drift, or other performance degradation. The seal welding process is a critical step in ensuring the long-term reliability of the crystal oscillator.
Step 6. Sealing Inspection
Following seal welding, a sealing inspection is conducted to verify the integrity of the hermetic seal. This step ensures that the crystal oscillator is adequately protected from environmental factors. Leak testing is a common method used to detect any leaks in the seal. Helium leak testing is often used for high-precision applications, as it can detect very small leaks.
The sealing inspection is a critical quality control step that ensures the reliability and longevity of the crystal oscillator. Any leaks in the seal can compromise the crystal’s performance and lead to premature failure. The inspection process is typically performed using automated equipment to ensure consistent and accurate results.
The sealing inspection is essential for maintaining the high standards of crystal oscillator manufacturing. It provides assurance that each unit is hermetically sealed and protected from environmental hazards. The inspection process is a key factor in ensuring the long-term reliability and performance of the crystal oscillator.
Step 7. Aging and Simulated Reflow Soldering
Aging and simulated reflow soldering are processes designed to stabilize the crystal oscillator’s frequency and ensure its reliability under thermal stress. Aging involves subjecting the crystal to elevated temperatures for an extended period, allowing the frequency to stabilize and any residual stress to be relieved. Simulated reflow soldering involves exposing the crystal to temperatures similar to those encountered during surface mount assembly.
The aging process is critical for achieving high frequency stability and minimizing frequency drift over time. The simulated reflow soldering process ensures the crystal can withstand the thermal stress of surface mount assembly without experiencing significant frequency shifts. These processes are essential for ensuring the long-term reliability and performance of the crystal oscillator.
Both the aging and simulated reflow soldering processes are conducted in controlled environments to ensure consistent results. The parameters of these processes, such as temperature and duration, are carefully selected based on the crystal’s specifications and application requirements. The goal is to induce any potential frequency shifts early in the manufacturing process, allowing for corrections before final testing and shipment.
Step 8. Marking
Marking involves applying identifying information to the crystal oscillator package. This information typically includes the manufacturer‘s name, part number, frequency, and date code. Laser marking, ink marking, and pad printing are common techniques used for marking. The marking process must be clear, legible, and durable to ensure the information remains visible throughout the crystal’s lifetime.
The marking information is essential for traceability and identification of the crystal oscillator. It allows for easy identification of the part number, frequency, and manufacturer, which is crucial for inventory management and troubleshooting. The marking process is typically automated to ensure consistent and accurate marking.
The durability of the marking is critical for ensuring the information remains legible under various environmental conditions. The marking process must be carefully controlled to prevent damage to the crystal package. The clear and durable marking is a key factor in ensuring the traceability and identification of the crystal oscillator.
Step 9. Final Testing
Final testing is the last stage of the crystal oscillator manufacturing process, where each unit is subjected to a comprehensive set of tests to verify its performance and reliability. This stage ensures that only high-quality crystal oscillators are shipped to customers. The final testing process typically includes frequency measurement, temperature testing, and electrical performance testing.
The final testing stage is a critical quality control step that ensures each crystal oscillator meets the required specifications. Any units that fail the final testing are rejected or reworked. The testing process is typically automated to ensure consistent and accurate results.
The data collected during final testing is used to generate a certificate of conformance, which provides assurance that the crystal oscillator meets the customer’s requirements. The final testing process is a key factor in ensuring the high quality and reliability of the crystal oscillators shipped to customers.
Get Crystal Oscillators Now
The crystal oscillator manufacturing process is a meticulous journey, from raw quartz selection and precise cutting to intricate packaging and rigorous testing. Each step ensures the final product’s accuracy and stability, vital for countless electronic applications. This complex process underlines the technology’s importance in modern electronics.
Understanding the manufacturing intricacies highlights the precision required to produce reliable crystal oscillators. From frequency calibration to environmental testing, every detail is crucial. This ensures that the oscillators meet the stringent demands of various industries, delivering consistent performance.
For high-quality wholesale crystal oscillators, look no further than Weishi Electronics. We offer a diverse range of reliable oscillators to meet your project’s needs. Visit our website today to explore our selection and benefit from our competitive wholesale pricing.