In the intricate world of electronic devices, failure analysis of components stands as a pivotal process. Understanding why and how components fail is imperative for engineers to enhance product reliability and performance.
This article delves into the depths of failure analysis of electronic components, shedding light on its significance, methodologies, common issues, and expert solutions.
Failure Analysis of Electronic Components
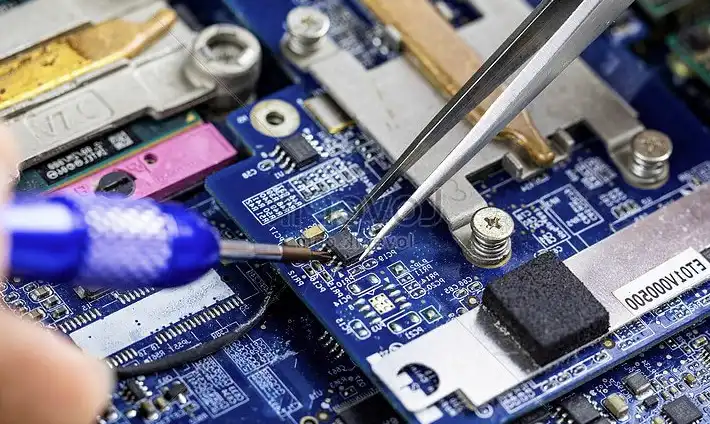
Failure analysis of electronic components is a multifaceted discipline aimed at identifying the root causes of component malfunction or breakdown. It involves meticulous investigation, testing, and evaluation to uncover underlying defects or weaknesses. By comprehensively dissecting failures, engineers gain invaluable insights to refine design, manufacturing processes, and quality control measures.
Electronic components have a wide range of failure modes. These can be classified in various ways, such as by time or cause. Failures can be caused by excess temperature, excess current or voltage, ionizing radiation, mechanical shock, stress or impact, and many other causes. In semiconductor devices, problems in the device package may cause failures due to contamination, mechanical stress of the device, or open or short circuits.
https://en.wikipedia.org/wiki/Failure_of_electronic_components
Importance of Failure Analysis
Failure analysis holds immense significance in the realm of electronic components and devices. It serves as a fundamental process for engineers and manufacturers, playing a crucial role in product development, quality assurance, and customer satisfaction.
Enhancing Product Reliability
One of the primary objectives of failure analysis is to enhance the reliability of electronic products. By identifying the root causes of failures, engineers can address design flaws, material weaknesses, or manufacturing defects that may compromise product performance. This proactive approach not only minimizes the risk of product failures but also instills confidence in consumers regarding the durability and longevity of electronic devices.
Improving Manufacturing Processes
Failure analysis provides valuable insights into the electronic component manufacturing processes employed in electronic component production. By analyzing failure modes and patterns, electronic component manufacturers can identify areas for improvement, optimize production techniques, and implement stringent quality control measures. This continuous refinement of manufacturing processes leads to higher yields, reduced defect rates, and ultimately, cost savings for companies.
Preventing Recurrence
One of the most significant benefits of failure analysis is its ability to prevent recurrence of failures in electronic devices. By understanding the underlying causes of failures, engineers can implement preventive measures and design enhancements to mitigate future risks. Whether it involves revising product specifications, modifying materials, or implementing additional testing protocols, failure analysis empowers manufacturers to proactively address potential vulnerabilities and ensure long-term product reliability.
Fostering Innovation and Advancement
Failure analysis fosters a culture of innovation and advancement in the electronics industry. By continually analyzing and learning from failures, engineers gain valuable insights that drive technological innovation and product development. These insights often lead to the discovery of new materials, design methodologies, or manufacturing techniques that push the boundaries of what’s possible in electronic device engineering. Ultimately, failure analysis fuels progress, driving the evolution of electronic components and devices towards greater efficiency, performance, and reliability.
Methodologies in Electronic Component Failure Analysis
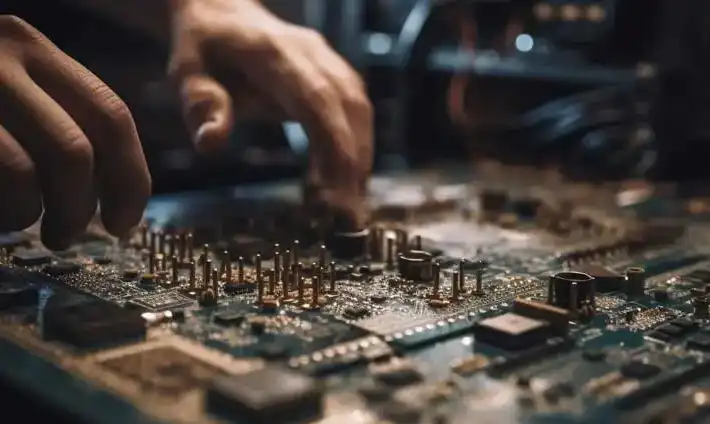
The process of electronic component failure analysis involves a systematic approach encompassing various methodologies aimed at uncovering the root causes of failures. These methodologies employ a combination of techniques ranging from non-destructive testing to detailed microstructural examination, each tailored to address specific aspects of failure investigation.
Non-Destructive Testing (NDT)
Non-destructive testing (NDT) techniques play a pivotal role in failure analysis by allowing engineers to assess the integrity of electronic components without causing damage. These techniques utilize advanced technologies such as X-ray inspection, thermal imaging, ultrasound, and acoustic microscopy to scrutinize components for defects, cracks, or anomalies. By providing insights into internal structures and material properties, NDT facilitates early detection of potential issues without compromising the physical integrity of components.
Destructive Testing
Destructive testing involves the physical dissection and examination of electronic components to gain deeper insights into failure mechanisms. Techniques such as cross-sectional analysis, microstructural examination, and chemical testing are employed to analyze the internal structure, composition, and material properties of components. While destructive testing irreversibly alters the tested specimens, it provides invaluable information regarding failure modes, material defects, or manufacturing irregularities that may contribute to component failures.
Electrical Testing
Electrical testing is integral to failure analysis as it enables engineers to evaluate the electrical performance of components under various operating conditions. By subjecting components to electrical stress tests, such as voltage, current, or temperature cycling, engineers can identify anomalies such as short circuits, open circuits, or electrical breakdowns. Additionally, specialized testing equipment, such as semiconductor parameter analyzers or curve tracers, facilitates the characterization of semiconductor devices, enabling engineers to pinpoint electrical failure mechanisms accurately.
Thermal Analysis
Thermal analysis plays a crucial role in failure analysis, particularly in assessing the thermal performance and reliability of electronic components. Techniques such as thermal imaging, infrared thermography, and thermal conductivity measurements are employed to identify thermal anomalies, hotspots, or thermal gradients within components. By correlating thermal data with electrical performance, engineers can diagnose issues related to thermal management, solder joint integrity, or thermal stress-induced failures.
Material Characterization
Material characterization techniques are utilized to analyze the composition, structure, and properties of materials used in electronic components. Techniques such as scanning electron microscopy (SEM), energy-dispersive X-ray spectroscopy (EDS), and atomic force microscopy (AFM) enable engineers to examine the morphology, crystal structure, and elemental composition of materials. Material characterization aids in identifying material defects, impurities, or metallurgical anomalies that may contribute to component failures.
Environmental Testing
Environmental testing simulates real-world operating conditions to assess the reliability of electronic components under various environmental factors such as temperature, humidity, vibration, or corrosive environments. Accelerated aging tests, thermal cycling tests, and humidity exposure tests are commonly employed to evaluate component performance and durability. Environmental testing helps identify vulnerabilities related to environmental stressors, enabling engineers to design robust components capable of withstanding harsh operating conditions.
Electronic Component Failure Modes
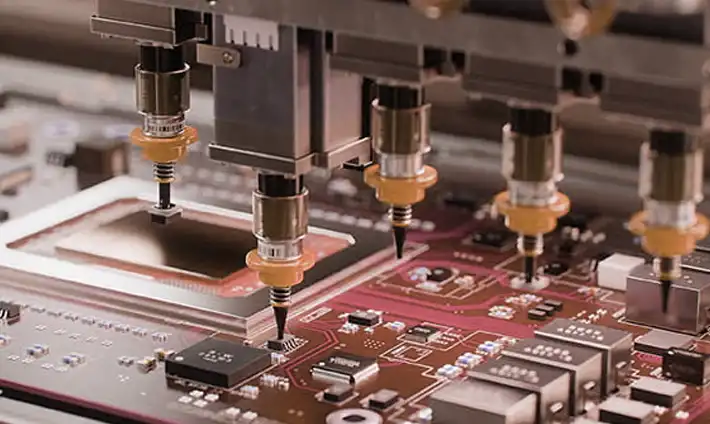
Electronic components are susceptible to a variety of failure modes that can occur due to factors such as mechanical stress, thermal cycling, electrical overstress, environmental factors, or manufacturing defects. Understanding these failure modes is essential for conducting effective failure analysis and implementing preventive measures to enhance component reliability.
Below are some common failure modes encountered in electronic components:
Mechanical Failure
Mechanical failure occurs when electronic components experience excessive stress, strain, or mechanical damage, leading to physical deformation, fractures, or mechanical wear. Common mechanical failure modes include:
- Fractures: Structural fractures or cracks in components due to mechanical shock, vibration, or flexural stress.
- Deformation: Permanent deformation or bending of components caused by excessive mechanical loading or thermal expansion mismatch.
- Wear: Surface wear or abrasion on component leads, terminals, or contact surfaces due to friction or mechanical rubbing.
Thermal Failure
Thermal failure arises from exposure to temperatures beyond the operating limits of electronic components, leading to degradation, thermal fatigue, or thermal runaway. Common thermal failure modes include:
- Solder Joint Failure: Weakening or failure of solder joints due to thermal cycling, solder fatigue, or excessive thermal stress.
- Dielectric Breakdown: Breakdown of insulating materials due to high temperatures, leading to short circuits or electrical arcing.
- Material Degradation: Degradation of component materials such as plastics, adhesives, or encapsulants due to prolonged exposure to elevated temperatures.
Electrical Overstress (EOS)
Electrical overstress (EOS) occurs when electronic components are subjected to electrical conditions beyond their specified limits, resulting in permanent damage or degradation. Common EOS failure modes include:
- Gate Oxide Breakdown: Breakdown of gate oxide layers in semiconductor devices due to high electric field or excessive voltage.
- Latch-Up: Abnormal conduction path formation in integrated circuits due to excessive current or voltage spikes.
- Electrostatic Discharge (ESD): Damage caused by electrostatic discharge events, leading to localized breakdown or junction damage in semiconductor devices.
Environmental Factors
Environmental factors such as humidity, moisture, dust, or corrosive substances can accelerate degradation or corrosion of electronic components, leading to premature failure. Common environmental failure modes include:
- Corrosion: Oxidation or corrosion of metal contacts, leads, or traces due to exposure to moisture, humidity, or corrosive gases.
- Mold Growth: Growth of mold or fungal colonies on component surfaces due to high humidity or poor environmental conditions.
- Contamination: Introduction of foreign particles, dust, or debris into electronic assemblies during manufacturing or operation, leading to electrical shorts or insulation breakdown.
Manufacturing Defects
Manufacturing defects such as inadequate soldering, material impurities, or process deviations can compromise the reliability of electronic components. Common manufacturing defect failure modes include:
- Poor Solder Joints: Incomplete or cold solder joints due to improper soldering techniques, leading to open circuits or intermittent connections.
- Material Impurities: Presence of contaminants, voids, or inclusions in component materials due to poor quality control or material handling practices.
- Process Deviations: Variations in manufacturing processes such as temperature, pressure, or time parameters, leading to inconsistent component performance or reliability.
Electronic components can fail due to a myriad of factors ranging from mechanical stress and thermal cycling to electrical overstress and environmental conditions. By understanding these failure modes and conducting comprehensive failure analysis, engineers can develop robust designs, improve manufacturing processes, and enhance the reliability of electronic devices.
The Time to Failure in Hours of an Electronic Component
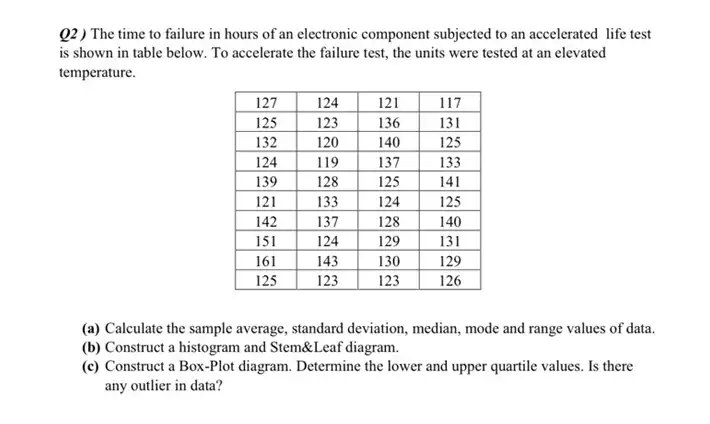
The time to failure in hours of an electronic component refers to the duration or lifespan of the component before it ceases to function properly or fails completely.
This metric is crucial for assessing the reliability and durability of electronic devices and systems. The time to failure can vary significantly depending on factors such as operating conditions, environmental stresses, component quality, and usage patterns.
Engineers often conduct reliability testing and analysis to estimate the time to failure and ensure that electronic components meet or exceed specified performance requirements and longevity expectations.
The Probability That a Certain Electronic Component Fails
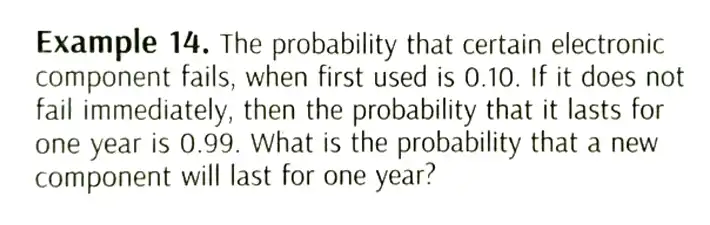
The probability that a certain electronic component fails is a crucial concept in engineering and reliability analysis. It represents the likelihood or chance that the component will experience a malfunction or cease to function within a given period.
This probability is often expressed as a percentage or a decimal value ranging from 0 to 1, where 0 indicates no chance of failure, and 1 indicates a certainty of failure.
Several factors influence the probability of failure for electronic components:
- Component Design: The design of the component plays a significant role in its reliability. Components engineered with robust designs, adequate margins, and suitable materials are less likely to fail prematurely.
- Manufacturing Quality: The quality of manufacturing processes can impact the reliability of electronic components. Components manufactured with high precision, stringent quality control measures, and adherence to industry standards are more reliable.
- Environmental Conditions: Environmental factors such as temperature, humidity, vibration, and contaminants can affect the reliability of electronic components. Components exposed to harsh environments may experience accelerated degradation and higher probabilities of failure.
- Operating Stresses: The operating conditions and stresses experienced by electronic components during use can impact their reliability. Components subjected to excessive electrical currents, voltage spikes, thermal cycling, or mechanical stresses are more prone to failure.
- Failure Modes: Different failure modes, such as mechanical failure, thermal failure, electrical overstress, or environmental degradation, contribute to the overall probability of failure. Understanding the predominant failure modes and their root causes is essential for mitigating risks and improving reliability.
To assess the probability of failure for electronic components, engineers utilize various reliability analysis techniques, including:
- Reliability Prediction Models: Statistical models and empirical data are used to predict the probability of failure based on component characteristics, operating conditions, and historical failure rates.
- Failure Rate Analysis: Failure rates, expressed as failures per unit of time, are analyzed to estimate the likelihood of failure within a specific timeframe.
- Weibull Analysis: Weibull distribution analysis is commonly used to model the probability of failure over time, taking into account factors such as infant mortality, wear-out, and random failures.
- Accelerated Life Testing: Accelerated life testing involves subjecting components to accelerated stress conditions to accelerate failure mechanisms and estimate failure probabilities within a shorter timeframe.
By quantifying the probability of failure, engineers can make informed decisions regarding component selection, design optimization, reliability improvement measures, and maintenance strategies to ensure the overall reliability and performance of electronic systems.
FAQs
What are the primary objectives of failure analysis?
The primary objectives include identifying root causes of failures, enhancing product reliability, improving manufacturing processes, and preventing recurrence.
How does failure analysis benefit electronic device manufacturers?
Failure analysis enables manufacturers to refine design, materials selection, manufacturing processes, and quality control measures, ultimately enhancing product reliability and customer satisfaction.
What are some common non-destructive testing techniques used in failure analysis?
Common non-destructive testing techniques include X-ray inspection, thermal imaging, ultrasound, and acoustic microscopy.
Can failure analysis prevent future failures in electronic devices?
Yes, failure analysis provides valuable insights to address vulnerabilities proactively, enabling manufacturers to implement preventive measures and design enhancements to mitigate future failures.
How does thermal failure affect electronic components?
Thermal failure can lead to solder joint failures, dielectric breakdown, material degradation, or component warping, compromising functionality and reliability.
What role does environmental testing play in failure analysis?
Environmental testing assesses component performance under various conditions such as temperature, humidity, vibration, and corrosive environments, simulating real-world operating conditions to identify potential failure modes.
Conclusion
In conclusion, failure analysis of electronic components is indispensable for ensuring product reliability, performance, and customer satisfaction in the ever-evolving landscape of electronic device manufacturing. By unraveling the mysteries behind component failures, engineers pave the way for innovation, quality improvement, and technological advancement.